So my battery arrived and I finally got some time to convert my bike using the Tongxin Goldant kit described in this thread. Thought I would document how I got on here in case anyone else finds it useful.
To recap, I wanted to add a light hub motor to my existing hybrid commuter bike (Specialized Sirrus) to make my 7 mile round trip commute (with a couple of hills) a bit quicker and easier.
I ordered the 190rpm motor with cables, a pedelec sensor and disc, and a throttle and LED battery guage from keyde.com. Their salesperson, Sky, was very helpful and responsive and my kit arrived within a couple of weeks. I went for the motor with built in controller for simplicity and had it drilled with 32 spoke holes. The whole kit cost around £180 delivered (the one with the separate controller is a bit cheaper).
The keyde.com bottle batteries were expensive (£350 plus) so I decided to order a 12s2p 4.6Ah A123 pack from cellman. This was significantly less expensive (about £250 including charger) and will hopefully last a decent length of time.
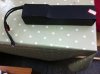
I went for a long, thin arrangement as I had originally planned to mount it on the frame somewhere. In the end though, I went for the easier option of just sticking it in one of my rear panniers.
Other miscellaneous bits I got mainly from e-bay: Anderson powerpole connectors, a length of 30A, 2-core automotive cable (to extend supplied power cord), lots of long, black cable ties, a tube of 5-minute epoxy, and some shrink wrap. The tools I used were: a round metal file, a dremel, an adjustable wrench, crimping pliers, some hex keys in various sizes, and a crank-puller. Most of these I had in the shed.
First job was to get the motor built into a wheel, which I entrusted to my local bike shop. I used a Mavic open sport rim. The wheel build cost £30 including spokes. I had to file the dropouts slightly to get the hub to fit. The front fork is aluminium, and I had been in two minds about the need to fit a torque arm to this low power setup but ended up glad I had ordered one as it gives me some extra reassurance that I haven't weakened things too much. I bought the £10 torque arm kit from cyclezee, which is both very strong and discrete.
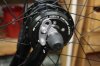
In it's original form, the power cable is only long enough to reach the middle of the top tube, so I needed and extension to reach the pannier. I cut off the original co-axial plug and crimped on Anderson powerpole connectors (assuming, as per Jerry Simon's previous thread, that the centre pin is positive).
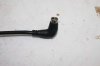
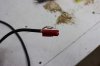
I attached this to my extension cable and covered the join with some shrink wrap and duct tape for weatherproofing.
Next step was the pedelec sensor, which was the only really problematic part of the whole build. I had to remove some plastic from the magnetic disc with the dremel to get it to fit between the crank and the bottom bracket.
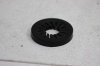
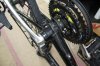
There are cables running under the bottom bracket shell, which limited the placement of the pedelec sensor. I had to cut a bit of the plastic housing away to make it shorter and then the first position I tried did not work - the motor kept cutting in and out so it wasn't getting a reliable signal.
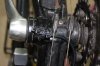
Fortunately, the epoxy was still soft when I figured this out, so I was able to peel it off and try again. This is the final position, which worked.
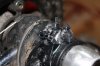
I secured the rest of the wires with cable ties and fitted the throttle control. The whole thing took me around four hours including various missteps along the way. I'm pretty happy with the finished product, which takes about five minutes each way off my commute and all the effort out of hill climbing (although you still have to pedal a bit).
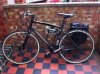
Overall, I would recommend this kit. Very low rolling resistance and easy to ride unpowered. My only niggles are the throttle, which is pretty cheap and fragile and which I doubt will survive the rigours of commuting for very long. It is also fairly pointless as others have observed - you have to be pedalling for the motor to cut in irrespective of the throttle position and the different levels of assistance virtually indistinguishable. An on/off switch would be more use.
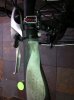
The pedelec sensor is also a bit indecisive around its cut-off cadence, although this may be because my positioning of the sensor is (still) not optimal.
I could probably have bought an off-the-shelf 8fun kit for similar outlay, but I liked the idea of this small discrete motor and have learnt quite a bit about these systems along the way, much of it from this forum so many thanks to you all.
To recap, I wanted to add a light hub motor to my existing hybrid commuter bike (Specialized Sirrus) to make my 7 mile round trip commute (with a couple of hills) a bit quicker and easier.
I ordered the 190rpm motor with cables, a pedelec sensor and disc, and a throttle and LED battery guage from keyde.com. Their salesperson, Sky, was very helpful and responsive and my kit arrived within a couple of weeks. I went for the motor with built in controller for simplicity and had it drilled with 32 spoke holes. The whole kit cost around £180 delivered (the one with the separate controller is a bit cheaper).
The keyde.com bottle batteries were expensive (£350 plus) so I decided to order a 12s2p 4.6Ah A123 pack from cellman. This was significantly less expensive (about £250 including charger) and will hopefully last a decent length of time.
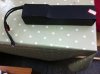
I went for a long, thin arrangement as I had originally planned to mount it on the frame somewhere. In the end though, I went for the easier option of just sticking it in one of my rear panniers.
Other miscellaneous bits I got mainly from e-bay: Anderson powerpole connectors, a length of 30A, 2-core automotive cable (to extend supplied power cord), lots of long, black cable ties, a tube of 5-minute epoxy, and some shrink wrap. The tools I used were: a round metal file, a dremel, an adjustable wrench, crimping pliers, some hex keys in various sizes, and a crank-puller. Most of these I had in the shed.
First job was to get the motor built into a wheel, which I entrusted to my local bike shop. I used a Mavic open sport rim. The wheel build cost £30 including spokes. I had to file the dropouts slightly to get the hub to fit. The front fork is aluminium, and I had been in two minds about the need to fit a torque arm to this low power setup but ended up glad I had ordered one as it gives me some extra reassurance that I haven't weakened things too much. I bought the £10 torque arm kit from cyclezee, which is both very strong and discrete.
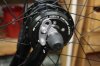
In it's original form, the power cable is only long enough to reach the middle of the top tube, so I needed and extension to reach the pannier. I cut off the original co-axial plug and crimped on Anderson powerpole connectors (assuming, as per Jerry Simon's previous thread, that the centre pin is positive).
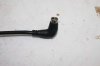
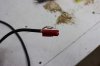
I attached this to my extension cable and covered the join with some shrink wrap and duct tape for weatherproofing.
Next step was the pedelec sensor, which was the only really problematic part of the whole build. I had to remove some plastic from the magnetic disc with the dremel to get it to fit between the crank and the bottom bracket.
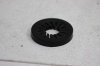
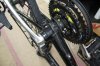
There are cables running under the bottom bracket shell, which limited the placement of the pedelec sensor. I had to cut a bit of the plastic housing away to make it shorter and then the first position I tried did not work - the motor kept cutting in and out so it wasn't getting a reliable signal.
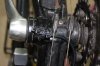
Fortunately, the epoxy was still soft when I figured this out, so I was able to peel it off and try again. This is the final position, which worked.
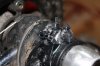
I secured the rest of the wires with cable ties and fitted the throttle control. The whole thing took me around four hours including various missteps along the way. I'm pretty happy with the finished product, which takes about five minutes each way off my commute and all the effort out of hill climbing (although you still have to pedal a bit).
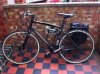
Overall, I would recommend this kit. Very low rolling resistance and easy to ride unpowered. My only niggles are the throttle, which is pretty cheap and fragile and which I doubt will survive the rigours of commuting for very long. It is also fairly pointless as others have observed - you have to be pedalling for the motor to cut in irrespective of the throttle position and the different levels of assistance virtually indistinguishable. An on/off switch would be more use.
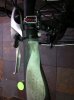
The pedelec sensor is also a bit indecisive around its cut-off cadence, although this may be because my positioning of the sensor is (still) not optimal.
I could probably have bought an off-the-shelf 8fun kit for similar outlay, but I liked the idea of this small discrete motor and have learnt quite a bit about these systems along the way, much of it from this forum so many thanks to you all.