I'm not really a mechanical guy so here we go...I noticed my rear hub was starting to spin out of dropout on drive side and didn't have a spanner to tighten it back up when I was out.
This is the current setup as it came back from bike guy I just wanted to check the order of where the dropout should go and QA what I got back from shop. I have read that the Axle nut should be on outside on drive side and NOT have a washer on the outside of dropout but I think when I got bike it did have washer on with the flat cutout outside as per the pic, it cannot go in inside as it will block the torque washer and stop it sitting in the dropout?
Can anyone clarify what the order should be to maximise the 'grip' in the drop out?
What is the nut that has a corner cut off it for, is it to stop the washer hitting the silver part on left dropout, is it required?
Is this setup recommended or are there better more secure ways? I guess threadlocker will make zero difference due to the forces involved?
I am working on a 3D Tinkercad design for drive side torque arm that will use the two screws on dropout that the old derailleur guard used to screw on to to stop this happening again. It will be two 1mm thick metal plates.
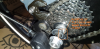
Also, is this OK for non-drive side? Dropout goes between torque nut (lined up properly) and torque arm?
Thanks
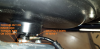
This is the current setup as it came back from bike guy I just wanted to check the order of where the dropout should go and QA what I got back from shop. I have read that the Axle nut should be on outside on drive side and NOT have a washer on the outside of dropout but I think when I got bike it did have washer on with the flat cutout outside as per the pic, it cannot go in inside as it will block the torque washer and stop it sitting in the dropout?
Can anyone clarify what the order should be to maximise the 'grip' in the drop out?
What is the nut that has a corner cut off it for, is it to stop the washer hitting the silver part on left dropout, is it required?
Is this setup recommended or are there better more secure ways? I guess threadlocker will make zero difference due to the forces involved?
I am working on a 3D Tinkercad design for drive side torque arm that will use the two screws on dropout that the old derailleur guard used to screw on to to stop this happening again. It will be two 1mm thick metal plates.
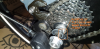
Also, is this OK for non-drive side? Dropout goes between torque nut (lined up properly) and torque arm?
Thanks
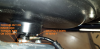