So here's what the circuit looks like. When I get a bit more time i'll sort a proper schematic out. But based on this diagram you should be able to work it out. The VCC needs 5v. I havnt bothered building in a switch since the whole circuit takes such little power its not worth it.
Here's some links to the IC's I used:
4013 D-Type Flip Flop http://www.electroschematics.com/6509/4013-datasheet/
4093 NAND http://www.electroschematics.com/6454/ic-4093-datasheet/
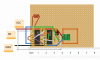
Here's some links to the IC's I used:
4013 D-Type Flip Flop http://www.electroschematics.com/6509/4013-datasheet/
4093 NAND http://www.electroschematics.com/6454/ic-4093-datasheet/
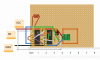