a torquesensor is for me a must have Item to get a normal bike-riding-feeling.
The bottom-braket-sensors make to much trouble in my eyes and the most of them have an old style square-tapered axle
as someone who crack those axle´s easy with my 150kg I have spend a lot of time in Hospital for those rubish crank´s.
So I was happy when I found Kclamber-Sensor in China and saw it is already used inside a few motor-brands and my Employer "Lishui-Controller" already have a controller for those motors. So I can use my shimano hollowtech-II crank or my ISIS crank
I bought all motors with those sensors that I could get a hold of and tested them. First to say it is the best solution so far for torquesensor Hub-Motor bikes but as an old school german technician there was always something to complain about, motor to noisy, to heavy, to unreliable, to weak and so on.
The best Motor during testing was the Aikema with this sensor but a 2kg motor is a bit to weak in my opinion so I asked Shengyi-Motor why they don´t implement this sensor into their "x2" Motor because it would be a perfect combo but their boss has zero interest into it so I did convert that shengyi-x2 Motor that I had in my office on my own into a Kclamber cassette Sensor motor
The result of my "X2" Motor conversion is exactly what I´ve expectet, a new benchmark for hubmotor pedelec, powerfull and noiseless. Noiseless is a very important point to me because when I´m riding a bike through nature I don´t want to hear anything from the motor. Some say "if you hear the sprockets it is not so bad" but for me it is nightmare
Advantage of the Kclamber sensor: only 3 connectors you need to connect to get a high level ebike with Torquesensor. Just Battery, display and Motor, there is nothing on the crank anymore. All is inside the hubmotor The Motor is connected by U-art to the controller and transmit all the time data-packages to the conntroller. The response of the sensor is way better and more sensitive as if you have a bottom-braket sensor.
I will search for more motors with this sensor when I fly to china hopefully somewhere in the next few weeks and if I find one that you can just plug and play I keep you posted
It is the future for better ebikes with hubmotor on a same level as well known centermotor from germany or japan
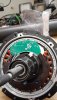
The bottom-braket-sensors make to much trouble in my eyes and the most of them have an old style square-tapered axle
So I was happy when I found Kclamber-Sensor in China and saw it is already used inside a few motor-brands and my Employer "Lishui-Controller" already have a controller for those motors. So I can use my shimano hollowtech-II crank or my ISIS crank
I bought all motors with those sensors that I could get a hold of and tested them. First to say it is the best solution so far for torquesensor Hub-Motor bikes but as an old school german technician there was always something to complain about, motor to noisy, to heavy, to unreliable, to weak and so on.
The best Motor during testing was the Aikema with this sensor but a 2kg motor is a bit to weak in my opinion so I asked Shengyi-Motor why they don´t implement this sensor into their "x2" Motor because it would be a perfect combo but their boss has zero interest into it so I did convert that shengyi-x2 Motor that I had in my office on my own into a Kclamber cassette Sensor motor
The result of my "X2" Motor conversion is exactly what I´ve expectet, a new benchmark for hubmotor pedelec, powerfull and noiseless. Noiseless is a very important point to me because when I´m riding a bike through nature I don´t want to hear anything from the motor. Some say "if you hear the sprockets it is not so bad" but for me it is nightmare
Advantage of the Kclamber sensor: only 3 connectors you need to connect to get a high level ebike with Torquesensor. Just Battery, display and Motor, there is nothing on the crank anymore. All is inside the hubmotor The Motor is connected by U-art to the controller and transmit all the time data-packages to the conntroller. The response of the sensor is way better and more sensitive as if you have a bottom-braket sensor.
I will search for more motors with this sensor when I fly to china hopefully somewhere in the next few weeks and if I find one that you can just plug and play I keep you posted
It is the future for better ebikes with hubmotor on a same level as well known centermotor from germany or japan
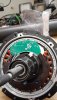
Attachments
-
785.8 KB Views: 16
Last edited: