Hello All. I have an Impulse Evo drive (bought it for a project) and would like to figure out where the brake sensors are supposed to be connected. There are 6 connectors sticking out from the unit. I thought the upper two would be for the two brakes, but it turned out they deliver 6V for the lights. The red plug, I don't know what for (maybe configuration?), there was a jumper inserted already. The big one is for the power and CAN bus, the next for display and the lower one is connected to the speed sensor and the shift wire sensor. But where are the brakes??? Will highly appreciate if someone could help me to resolve this puzzle.
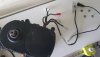
I
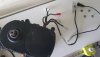
I