My Q100H has just arrived from BMS, with the usual quick delivery service, just over a week since ordering.
However, the spokes I ordered with it do not fit in the spoke holes correctly.
I ordered forty 260mm long 13g stainless steel spokes with the hub.
I just tried putting them in, and couldn't get them round the elbow at the end, even with moderate jiggling about. I looked at them a bit more closely, and found that the elbow was too short for the thickness of the spoke holes in the Q100 hub. On closer inspection, they'd sent me 42 spokes in all, and one of them had a slightly longer elbow, which slips easily into the hub flange, turning easily round the bend, right up to the stop.
Presumably, they've sent me the wrong spokes, designed for a much thinner hub flange ?
The only parameters you can specify when ordering are the spoke length and the gauge (diameter). They're bang on the length ok, (260mm), and the diameter is 2.2mm, so they're pretty much 13 gauge.
Anyone had this before ? I guess I'll have to email them and see what they say.
( I ordered the 260mm ones in the end Dave, because I have another 700c rim, which they will fit ok).
Here's a photo of the one spoke that's ok, and one of the other forty one !!
Damn ! I was really looking forward to building my first wheel, now I'll have to wait another ten days at least....
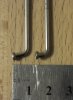
However, the spokes I ordered with it do not fit in the spoke holes correctly.
I ordered forty 260mm long 13g stainless steel spokes with the hub.
I just tried putting them in, and couldn't get them round the elbow at the end, even with moderate jiggling about. I looked at them a bit more closely, and found that the elbow was too short for the thickness of the spoke holes in the Q100 hub. On closer inspection, they'd sent me 42 spokes in all, and one of them had a slightly longer elbow, which slips easily into the hub flange, turning easily round the bend, right up to the stop.
Presumably, they've sent me the wrong spokes, designed for a much thinner hub flange ?
The only parameters you can specify when ordering are the spoke length and the gauge (diameter). They're bang on the length ok, (260mm), and the diameter is 2.2mm, so they're pretty much 13 gauge.
Anyone had this before ? I guess I'll have to email them and see what they say.
( I ordered the 260mm ones in the end Dave, because I have another 700c rim, which they will fit ok).
Here's a photo of the one spoke that's ok, and one of the other forty one !!
Damn ! I was really looking forward to building my first wheel, now I'll have to wait another ten days at least....
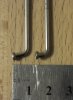